Choosing The Right Band Saw Blade
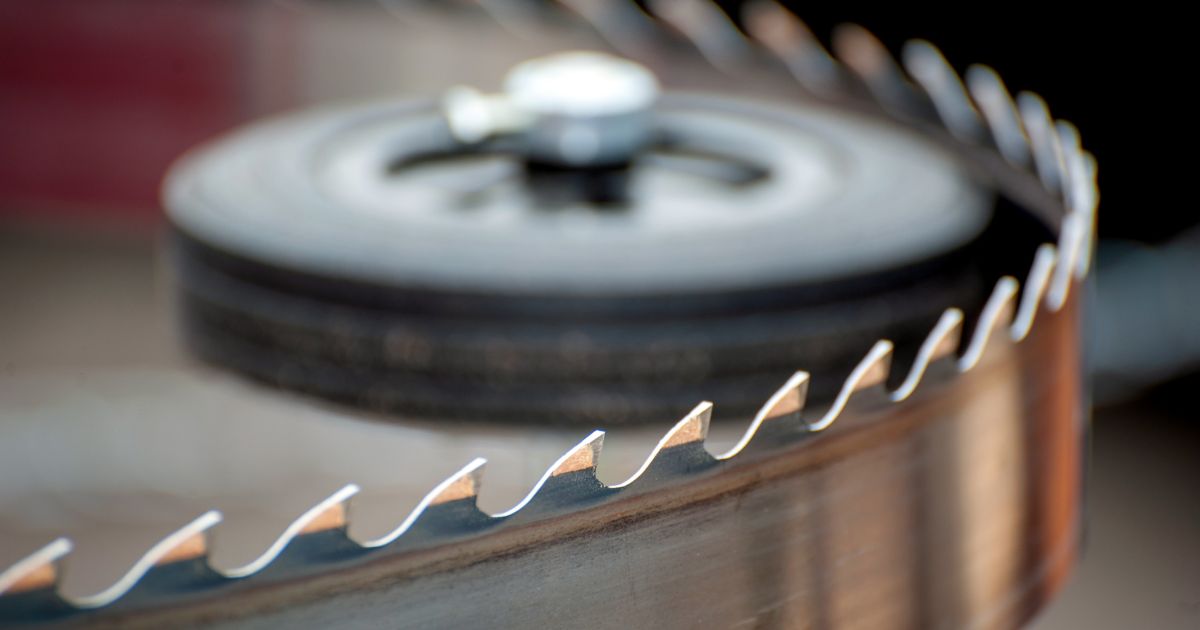
- How to know when it's time to replace your band saw blades
- Possible specific issues with your current saw blade
- Key factors to consider when making your purchase (such as the material to cut, blade dimension, blade teeth specifications and types, blade brand, intended use etc)
How to know when it's time to replace your band saw blades
Symptoms you can check through visual inspection:
- Blade wear: Check for chipped, broken or worn teeth. Dull blades show signs of wear on the tips and edges of the teeth.
- Chipped or broken teeth: Examine the teeth closely for any damage like chips, cracks, or worn tips. These indicate the blade is dull and can tear or burn your material instead of cutting smoothly.
- Uneven or rough cuts: Dull blades often produce ragged, wavy, or uneven cuts with burn marks on the edges.
- Rust or corrosion: While some surface rust can be cleaned, extensive damage weakens the blade and increases the risk of snapping.
Noticeable performance changes:
- Increased cutting effort: If you need to push harder than usual to feed the material through the saw, it could be due to a dull blade, that is a strong indicator of a dull blade that needs replacement.
- Slower cutting speed: A dull blade takes longer to cut through the same material, thereby reducing your efficiency.
- Excessive noise or vibration: An unusual screeching or vibrating sound while cutting can indicate a dull blade or other issues.
Other factors:
- Burning smell: This can occur due to increased friction from a dull blade, heating up the material and blade itself.
- Blade type: Different blade types have different lifespans, with finer teeth wearing out faster than coarse ones.
- Material being cut: Harder materials wear down blades faster than softer ones.
- Frequency of use: Blades naturally wear down with use, so replace them more often if you use your bandsaw frequently.
As a general rule, consider replacing your bandsaw blade regularly, even if it doesn't show obvious signs of wear. Experts recommend changing blades every 50-100 hours of use or after completing a specific project.
Possible specific issues with your current band saw blade
According to this Excision article (which by the way has useful illustration videos), here are the top five things you may want to inspect:
Problem (Symptoms) | Solution |
Tooth pitch is too coarse:
|
Use a blade with finer tooth pitch. (The optimal TPI is 5-7 teeth in the cut.) |
Tooth pitch is too fine:
|
Use a blade coarser tooth pitch. (By the way, you can reduce chances of aluminium swarf sticking to the blade with this Excision Lube Stick.) |
Worn side guides:
|
Clean the side guides, check for proper alignment / pressure and adjust as needed. |
Worn back guides:
|
Replace the worn back guides. |
Worn damping rollers:
|
Reduce the contact pressure so the damping rollers can rotate with little effort. Replace the rollers. |
This table from Excision makes it really easy for everybody:
Key factors to consider when making your purchase
Material you'll be cutting
- Wood: Most common blade types for wood include carbon steel, bi-metal and carbide-tipped. Choose based on wood type (hardwood or softwood), desired cut finish and frequency of use.
- Metal: Blades specifically designed for metal will be made from stronger materials like cobalt or bi-metal with carbide teeth. Consider the metal type (ferrous or non-ferrous), thickness and desired cut quality.
- Other materials: Blades exist for plastics, composites and even food, so make sure to get the appropriate blade type accordingly.
Blade dimensions
Here’s an illustration of the width, length and tooth per square inch (TPI) as taken from the Excision catalog:
- Length: While most blades come in standard length (with custom lengths also available), you should still ensure to match it to your bandsaw's specifications. A popular way to do this is to (1) mark a spot on the blade, (2) lay out a tape measure on a flat surface, (3) align the mark on the blade with the beginning of the tape measure, then (4) slowly roll the blade along the tape, keeping it flat and aligned, then you (5) continue rolling until you reach a full circle and the mark comes back, and finally (6) take note of the reading when it touches the tape again. That is your blade length. (The may in this video also shows how to do it.)
Another option is to measure it this way, as illustrated by Excision:
- Width: Narrower blades (1/4" to 1/2") offer tighter turning radii for intricate cuts, while wider blades (3/4" to 1") provide better stability for straight cuts and resawing. Blade width is measured from the tip of the blade to the back of the blade.
- Thickness: Thicker blades handle thicker materials and heavy use but are less flexible. Thinner blades are more flexible for curves but may break easier.
- Tooth pitch: Refer to the next section.
Blade teeth
- Teeth per inch (TPI): Higher TPI means more teeth and smoother cuts, ideal for detailed work. Lower TPI means fewer teeth and faster cuts, suitable for rough cuts or bulk material removal.
- Tooth configuration: Standard teeth are versatile, skip teeth are good for soft materials, and hook teeth excel in hard or thick materials.
- Set: Refers to how much each tooth is bent outward. A wider set increases chip clearance but reduces blade stability; a narrower set provides finer cuts but risks clogging.
Blade teeth types
Type | Shape | Gullet | Best for | Pros | Cons |
---|---|---|---|---|---|
Regular | Straight, evenly spaced teeth | Deep and wide | Thin materials, general purpose cutting (straight & curved), wood & some metals | Smooth cuts, versatile | Not ideal for thick materials or fast cuts |
Hook | Hook-shaped, widely spaced with prominent undercuts | Deep and wide | Thick materials, fast cuts, long cuts (gullet aids chip removal) | Efficient chip removal, aggressive cutting | Rougher cuts, not ideal for thin materials or tight curves |
Skip | Similar to hook tooth, but with straight cutting edge and even wider spacing | Deep and wide | Soft materials (plastics, non-ferrous metals) to prevent clogging | Minimizes clogging, clean cuts | Less aggressive than hook tooth, not ideal for hard materials or thick cuts |
Variable | Combination of different tooth sizes and shapes in a repeating pattern | Variable depths based on tooth size | Variety of materials and cutting tasks, balancing aggression and smoothness | Versatile, efficient at different cut speeds and materials | More expensive than other types |
Wavy | Teeth arranged in a wave-like pattern, angled left and right in groups | Deep and wide | Thin sheet metal, tubes, and profiles | Smooth, clean cuts on thin metal, reduces vibrations | Not suitable for thick materials or wood |
Disclaimer: These are just general descriptions. The best type of blade for your project depends on the specific material, desired cut quality and your bandsaw's capabilities. Always consult the manufacturer's recommendations and choose the blade that best suits your needs.
Other factors
- Quality: Higher-quality blades made from better materials will last longer and offer cleaner cuts. Consider your budget and project demands.
- Brand: Different brands offer varying quality and price points. Research reputable brands based on your needs and budget. We’d recommend you try Excision band saw blades, as they are known for their excellent quality and wide range of products for various applications. (By the way, these blades are sharp! You may want to grab some cut-resistant gloves for when you handle them.)
- Application: Specific applications, such as re-sawing or metal cutting, may require specialised blade features, so keep in mind your intended use.
The best band saw blade is the one that perfectly matches your material, project requirements and budget. By considering these factors, you can make an informed choice that optimises your cutting experience.
By being attentive to these signs and following general guidelines, you can ensure your band saw runs smoothly and efficiently and avoid potential safety hazards caused by a broken or dull blade. It's also a good idea to keep a spare blade on hand so you can quickly replace a worn one, unless you want to deal with too much unplanned downtime.
AIMS' Note on Safe Use of Power Tools
- Inspection: Before using any tool, carefully inspect it for cracks, chips, loose handles, worn / mushroomed heads or any other signs of damage. Damaged or defective tools may cause harm! Ensure all guards are in place.
- Right tool for the job: Make sure you understand the intended purpose of each tool and choose the correct one for your specific job. Don't try to make a screwdriver work as a pry bar or a wrench as a hammer.
- Safe handling: Carry sharp tools pointed down and away from your body. Never carry tools in your pockets where they can cause injury. When passing a tool to someone, extend the handle first.
- PPE: Wear safety glasses or goggles to protect your eyes from flying debris. Consider gloves depending on the tool and task to prevent cuts or blisters but without compromising comfort, dexterity and protection. If working with noisy tools, wear ear protection.
- Maintenance: Keep your tools clean, sharp and properly maintained. Store them in a safe and organised place when not in use.
- During use: Maintain a firm grip and good balance while using the tool. Avoid distractions and focus on the task. Don't force the tool; let it work at its own pace. Keep cords clear of the cutting path and away from heat or sharp objects. Never leave a running tool unattended. When finished, turn the tool off, unplug it, and wait for any moving parts to stop completely before cleaning or making adjustments.