Choosing the Right Tap for Your Drilling Application
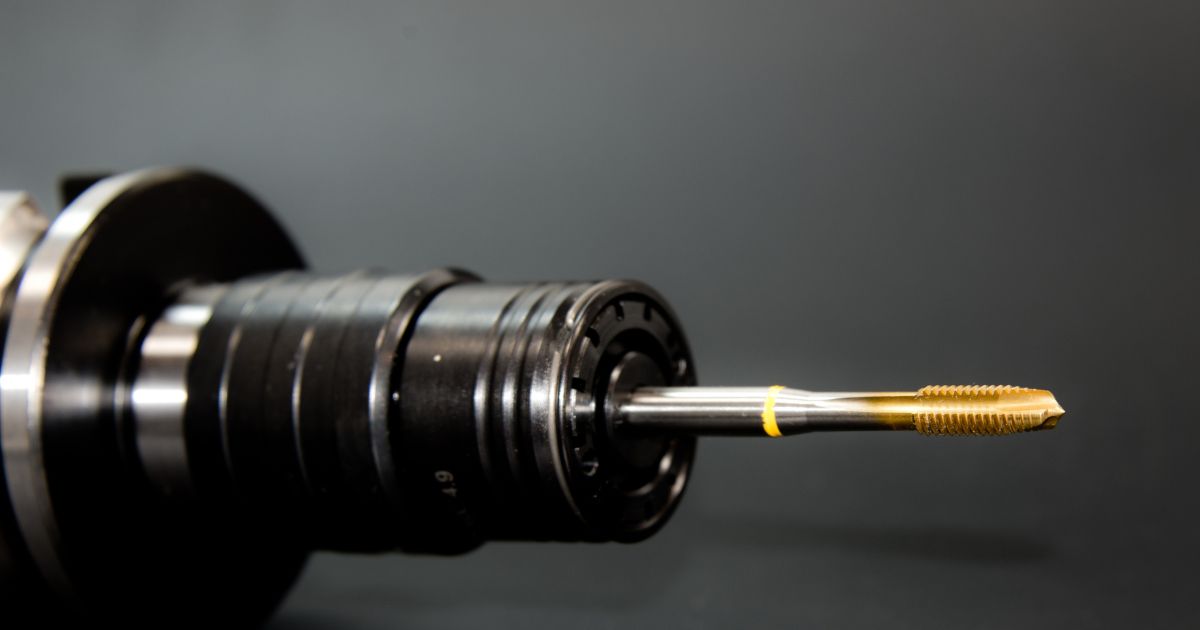
Whether you’re cutting new threads or repairing old ones, understanding your options can make a significant difference to the outcome. Here’s a brief guide to help you select the best tap for your needs.
Key features of a drill tap
- Fluted body: This allows for the removal of metal chips during the tapping process.
- Tapered or straight shank: The shank determines how the tap is held in a tap wrench.
- Thread profile: This matches the type of thread you want to create (eg metric, UNC, UNF).
- Chamfered tip: The beginning of the tap is often chamfered to facilitate starting the cutting process.
Types of taps
A tap is a precision-engineered cutting tool used to create internal threads in a drilled hole. Essentially, it’s a threaded rod with cutting edges that form mating threads in the workpiece when rotated. This process is known as tapping.
Tap sets for most threading applications contain:
- Taper tap: This is the first tap you use, and it initiates the thread by gradually cutting into the hole. It has a longer tapered section for easier entry.
- Plug tap: Following the taper tap, you can use this tap to continue cutting the threads deeper into the hole. It has a shorter taper than the taper tap.
- Bottoming tap: Designed to produce full threads to the bottom of the hole, this tap has minimal taper and full-length cutting threads.
Tap flute design (significantly impacts a tap's performance):
- Straight flute taps: Best suited for through-holes in soft materials like aluminium (aluminum) and brass, these taps offer good chip removal. While generally good in terms of chip removal, they may struggle with chip clearance in tougher materials.
- Spiral flute taps: Ideal for blind holes and materials producing long chips (like steel), these efficiently clear chips (by essentially pulling them out of the hole), thus reducing breakage and improving accuracy.
Other tap types
- Machine taps: Built for machine use, these taps are more rigid with longer flute lengths for efficient cutting.
- Hand taps: Designed for manual tapping, hand taps are typically made from high-carbon steel for durability.
Tap materials
The material of the workpiece will influence the tap’s material and flute design. Harder materials require taps with stronger flute geometries and coatings.
- High-speed steel taps: HSS taps are the most common and versatile, offering good performance in a wide range of materials. They’re tough and can handle high temperatures, making them suitable for most general-purpose threading tasks.
- Cobalt steel taps: For working with hard materials such as stainless steel, cobalt steel taps provide better wear resistance and durability. They maintain sharpness longer and can handle higher temperatures, making them ideal for tougher jobs and materials.
- Carbide taps: Carbide taps are incredibly hard and wear-resistant, ideal for high-precision work and tough materials. However, they are more brittle than HSS or cobalt taps and can break under stress, so they’re best used with appropriate tooling and techniques.
Tap coatings
Coated taps typically reduce friction and improve chip removal:
- Black oxide coating: This coating reduces friction and improves the tap’s resistance to wear and corrosion. It’s a good option for general-purpose applications where a combination of durability and performance is needed.
- Titanium nitride (TiN) coating: TiN-coated taps have a hard, wear-resistant surface that reduces friction and increases tool life. They are ideal for high-speed machining and materials that cause excessive wear.
- Zinc coating: Often used for taps that need to resist corrosion, zinc-coated taps are suitable for working in environments where exposure to moisture or chemicals is a concern.
More considerations
Aside from tap type, material and coating, here are other important things that will factor into your selection:
- Thread type: Determine the thread standard (eg metric, UNC, UNF) and the thread pitch (distance between threads). Common thread types include coarse thread series (UNC), fine thread series (UNF) and metric thread series.
- Hole type: Whether the hole is through or blind will determine the tap type. For blind holes, bottoming taps are often used to achieve full threads near the bottom.
- Hole size: The diameter of the drilled hole should be slightly smaller than the tap size to allow for thread formation. Tap drill charts provide recommended drill sizes for specific tap sizes.
- Tap material: Taps are typically made from high-speed steel (HSS), cobalt steel, or carbide.
- Tap flute design: The flute design affects chip evacuation and tap life. Spiral flutes are generally preferred for efficient chip removal.
Additional tips
- Use a tap and drill set: This ensures compatibility between the drill bit and tap.
- Lubricant: Applying cutting fluid or lubricant reduces friction and improves tap life.
- Tap speed: The correct tap speed is essential for preventing breakage.
- Coolant: Use coolant for tougher materials to prevent overheating.
- Reverse rotation: Occasionally reverse the tap to break chips free.
By carefully considering these factors, you can select the appropriate tap for your drilling application, ensuring optimal thread quality and tool life. Choosing the right tap can greatly affect the quality and efficiency of your threading tasks. By understanding the types, materials, coatings and options available, you can select the best tap for your specific needs and ensure high-quality results every time.
AIMS' Note on Safe Use of Power Tools
- Inspection: Before using any tool, carefully inspect it for cracks, chips, loose handles, worn / mushroomed heads or any other signs of damage. Damaged or defective tools may cause harm! Ensure all guards are in place.
- Right tool for the job: Make sure you understand the intended purpose of each tool and choose the correct one for your specific job. Don't try to make a screwdriver work as a pry bar or a wrench as a hammer.
- Safe handling: Carry sharp tools pointed down and away from your body. Never carry tools in your pockets where they can cause injury. When passing a tool to someone, extend the handle first.
- PPE: Wear safety glasses or goggles to protect your eyes from flying debris. Consider gloves depending on the tool and task to prevent cuts or blisters but without compromising comfort, dexterity and protection. If working with noisy tools, wear ear protection.
- Maintenance: Keep your tools clean, sharp and properly maintained. Store them in a safe and organised place when not in use.
- During use: Maintain a firm grip and good balance while using the tool. Avoid distractions and focus on the task. Don't force the tool; let it work at its own pace. Keep cords clear of the cutting path and away from heat or sharp objects. Never leave a running tool unattended. When finished, turn the tool off, unplug it, and wait for any moving parts to stop completely before cleaning or making adjustments.