Common Causes of Electric Motor Breakdown
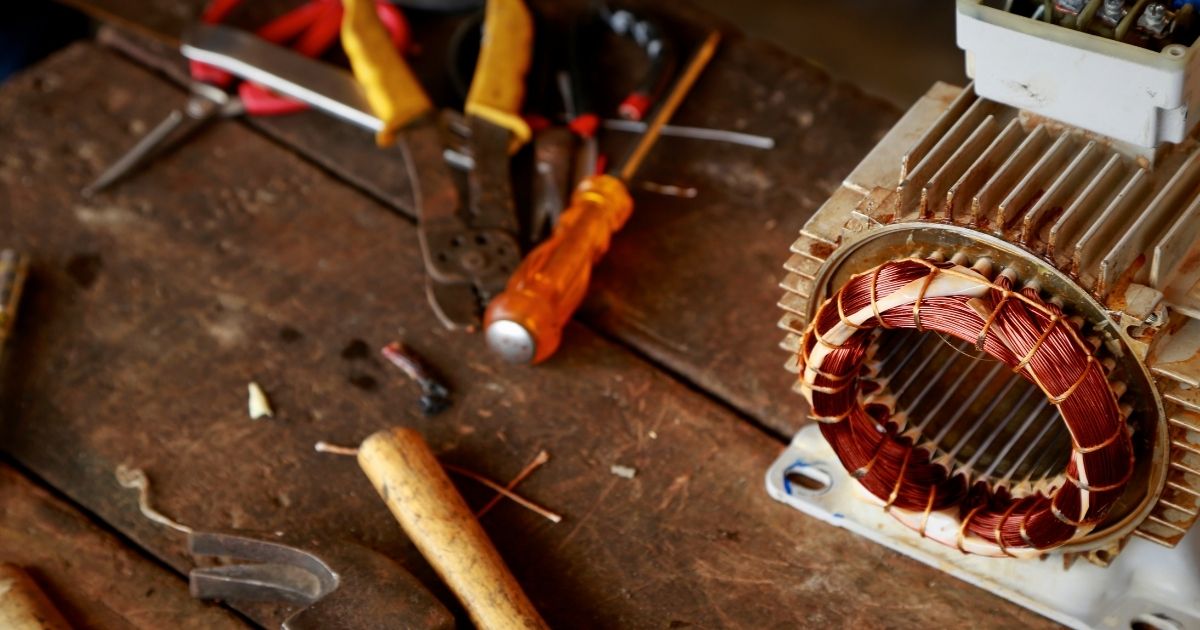
Here are some of the most common causes:
Bearing issues account for around 50% of failures and is the leading cause of motor breakdowns that are often associated with:
- Improper lubrication: Insufficient or wrong type of lubricant can lead to friction and wear.
- Contamination: Dirt, dust or moisture can enter them and cause damage.
- Excessive loads: Applying load greater than what the motor is rated for can put undue stress on them.
- Normal wear and tear: Like any mechanical component, they wear over time and need replacement.
Winding failures typically cause:
- Overheating: This can damage the insulating layer, leading to shorts and ultimately to burnout. Common causes include overload, poor ventilation or blocked cooling passages.
- Voltage spikes or fluctuations: Unstable power supply can harm insulation. Surge protectors and voltage regulators can help prevent this.
- Moisture or contamination: These can degrade insulation and cause malfunctions.
- Abrasion or physical damage: Mechanical impact or foreign objects that enter the motor can damage windings, so ensure your motor has the right ingress protection (IP) rating for your application.
External factors typically caused by:
- Overloading: Operating the motor beyond its rated capacity can lead to overheating and premature failure.
- Vibration: Excessive vibration from unbalanced loads or misalignment can stress components and lead to breakdowns.
- Improper installation: Incorrect mounting or alignment can put undue strain on the motor.
- Immediate environment: Exposure to environments with harsh conditions such as extreme temperatures, dust or corrosive chemicals can accelerate wear and tear of the motor and its components.
Other less common causes:
- Rotor issues: Unbalanced rotors, shaft cracks or excessive magnetic pull can occasionally cause problems.
- Low resistance: Issues like corrosion or overheating can weaken insulation, causing shorts and leaks.
- Voltage imbalance and fluctuation: The former has a more specific effect on multi-phase motors, while the latter can affect all types of motors. We discussed more about them in our other article on electric motor lifespans.
Proper maintenance -- including regular inspections, lubrication and cleaning -- can significantly extend the motor’s lifespan, reduce the risk of breakdowns and consequently help you prevent unplanned downtimes.
Most importantly, make sure you have the right one for the job. We put together a quick guide to help you choose the appropriate electric motor for your application.
It's always wise to follow best practice, consult the manufacturer's recommendations for proper electric motor care and implement proper preventive measures.
AIMS' Note on Safe Use of Belt-Driven Systems
- Power down: Before any inspection, maintenance, or adjustment, make sure to completely shut down the power to the machine and apply a lockout/tagout (LOTO) device to prevent accidental restarts.
- Right belt for the system: Keep in mind that v-belts (especially cogged / notched / wrapped belts) are different from synchronous /timing / ‘toothed’ belts. Some mistake the cogs for teeth but remember that cogged belts run on V-shaped pulleys that do not have teeth. Are you operating where flammable substances are present? Maybe you need fire-resistant anti-static (FRAS) belts – or maybe heat-resistant and oil-resistant belts will do. We compared them in this FAQ.
- Safe attire: Avoid loose clothing, jewelry and long hair that could get caught in the moving parts. Ensure proper fit of workwear without compromising comfort, dexterity and protection. Tie back long hair and secure loose items.
- Safeguards in place: Never operate a belt-driven system with the guards removed or bypassed. These guards are there for your protection.
- Maintenance and replacement: Regularly inspect belts and pulleys for wear and tear. Maintain proper belt tension and alignment as specified by the manufacturer. When replacing the belt, make sure you get the proper fit and measurement of the system. These accessories and maintenance kits (eg alignment tools, belt measurers, pulley gauge sets, spacers, tensioners etc) come in handy.
- Cleanliness: Keep the area around belt drives free of debris and clutter that could get caught or cause a fire hazard.
(Refer to our content library's sub-index of articles about belt-driven systems and electric motors for more information.)