Factors Affecting Electric Motor Lifespan
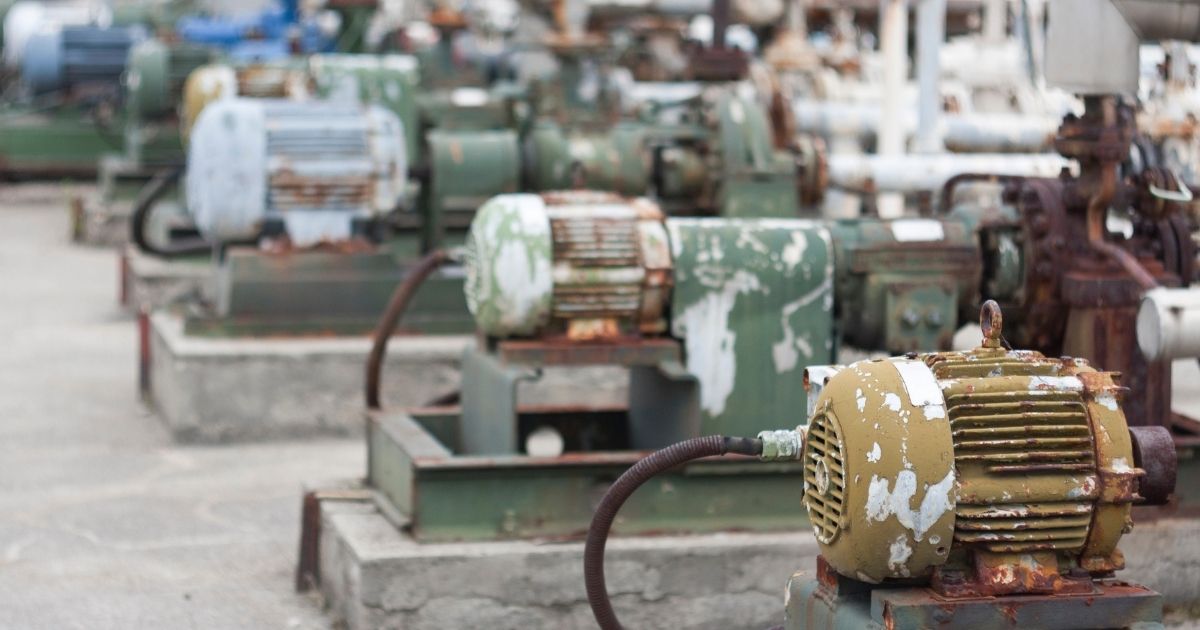
Figuring out the average lifespan and usability of an electric motor is complicated, but you can make an informed decision based on these factors:
Type of motor: Different motor types have different lifespans. For example, small DC motors used in appliances may last up to five years, while large industrial AC motors can last for decades with proper care. Choosing the right electric motor is critical, so make sure to read this quick guide to help you choose the right one.
Kilowatt / Horsepower rating relative to load: If you are familiar with the concept of power-to-weight ratio in automobiles, then this one closely relates to it. If you have too small a motor for too big a load (than its rated capacity), it will have a hard time doing its job. Some people think that a ‘slightly overpowered / oversized’ motor can help with any application, as it gives you some room for ‘extra operational capacity’ when you need to handle the occasional added load.
- Note: According to this factsheet titled Optimizing Your Motor-Drive System from the US Department of Energy (Power Quality, Article 13): “Size motors to run primarily in the 65% to 100% load range. Consider replacing motors running at less than 40% load with properly sized motors. You can address applications with occasional high peak loads by a variety of design strategies including adjustable speed drives (ASDs) ...”
Usage: How much and how hard the motor is used significantly affects its efficiency, longevity and usability. Constant -- and even continuous -- heavy-duty operation will naturally shorten its life compared to light, infrequent use.
Operating conditions: Environmental factors such as dust, humidity, temperature and vibration can affect the lifespan of the motor. Harsh conditions can lead to faster wear and tear. You may also want to consider what ingress protection (IP) rating applies to your intended use. When operating in hazardous areas, make sure to get the right one designed for such conditions.
Maintenance: Regular maintenance -- such as checking for bearing and pulley alignment, worn brushes and lubrication levels -- can significantly extend its lifespan. Note that some motors have a self-lubricating feature that only requires you to top up the oil wells occasionally.
Voltage imbalances and fluctuations: While both voltage imbalance and voltage fluctuation can adversely affect electric motor performance and lifespan, they are two distinct phenomena with different characteristics and impact as described below:
|
Voltage imbalance |
Voltage fluctuation |
What is it |
Unequal voltage magnitudes or phase angles between phases in a multi-phase system (eg in three-phase AC motors) |
Variation in voltage magnitude over time, regardless of phase |
Timeframe |
Can be a persistent issue that lasts for hours or days |
Can be short-term (milliseconds) or long-term (hours), depending on the cause |
Causes |
Single-phase loads on multi-phase systems, unequal line impedances, issues within the motor windings |
Load changes, grid instability, faults, short circuits, reactive power imbalance |
Impact on motor |
Increased heat generation (overheating), higher losses, torque pulsations, vibration, reduced efficiency, premature motor failure |
Motor stalling, torque variations, speed variations, overheating, tripping of overload protection |
Severity |
Even small levels (2-3%) can be detrimental |
Depends on size, duration and motor characteristics |
Measurement |
Requires specialised instruments, such as power analyzers |
Can be monitored with voltmeters and data loggers |
Mitigation |
Load balancing, phase balancing transformers, variable speed drives |
Voltage regulators, UPS systems, improved grid infrastructure |
Essentially, voltage imbalance has a more specific effect on multi-phase motors, while voltage fluctuation can affect all types of motors. Understanding the differences between these issues is crucial for proper motor diagnosis and mitigation strategies.
Although variable frequency drives (VFDs) such as Inverteks cannot directly prevent voltage imbalances, they can still help mitigate the negative effects of voltage fluctuations to your electric motor.
How VFDs help with voltage fluctuations:
- Built-in protection: Many VFDs have built-in features like undervoltage, overvoltage and brownout protection. These features can help protect the motor from damage caused by voltage fluctuations by shutting it down or limiting its operation under unsafe conditions.
- Controlled voltage output: VFDs can regulate the voltage output to the motor, providing a more stable and consistent level even if the input voltage fluctuates slightly. This can help reduce stress on the motor and improve its lifespan.
Limitations on voltage imbalances:
- No direct correction: VFDs do not directly address voltage imbalances between phases. They run on the incoming voltage and cannot actively balance it out.
- Potential masking: While VFDs might regulate the overall voltage to the motor, the imbalanced currents within the motor itself can persist and possibly cause harm.
For minor imbalances, VFDs might offer some protection against their indirect effects, however for severe imbalances, they are not a substitute for addressing the issue at the source of the power supply.
Addressing the imbalance at its source through the power supply or additional equipment remains crucial for optimal motor protection.
As we always recommend, if in doubt:
- Err on the side of caution.
- Consult with a qualified electrical professional to determine if a VFD is suitable for your specific application and level of voltage imbalance.
- Consult the VFD manufacturer's recommendations.
AIMS' Note on Safe Use of Belt-Driven Systems
- Power down: Before any inspection, maintenance, or adjustment, make sure to completely shut down the power to the machine and apply a lockout/tagout (LOTO) device to prevent accidental restarts.
- Right belt for the system: Keep in mind that v-belts (especially cogged / notched / wrapped belts) are different from synchronous /timing / ‘toothed’ belts. Some mistake the cogs for teeth but remember that cogged belts run on V-shaped pulleys that do not have teeth. Are you operating where flammable substances are present? Maybe you need fire-resistant anti-static (FRAS) belts – or maybe heat-resistant and oil-resistant belts will do. We compared them in this FAQ.
- Safe attire: Avoid loose clothing, jewelry and long hair that could get caught in the moving parts. Ensure proper fit of workwear without compromising comfort, dexterity and protection. Tie back long hair and secure loose items.
- Safeguards in place: Never operate a belt-driven system with the guards removed or bypassed. These guards are there for your protection.
- Maintenance and replacement: Regularly inspect belts and pulleys for wear and tear. Maintain proper belt tension and alignment as specified by the manufacturer. When replacing the belt, make sure you get the proper fit and measurement of the system. These accessories and maintenance kits (eg alignment tools, belt measurers, pulley gauge sets, spacers, tensioners etc) come in handy.
- Cleanliness: Keep the area around belt drives free of debris and clutter that could get caught or cause a fire hazard.
(Refer to our content library's sub-index of articles about belt-driven systems and electric motors for more information.)