FAQs on Electric Motors for Hazardous Areas
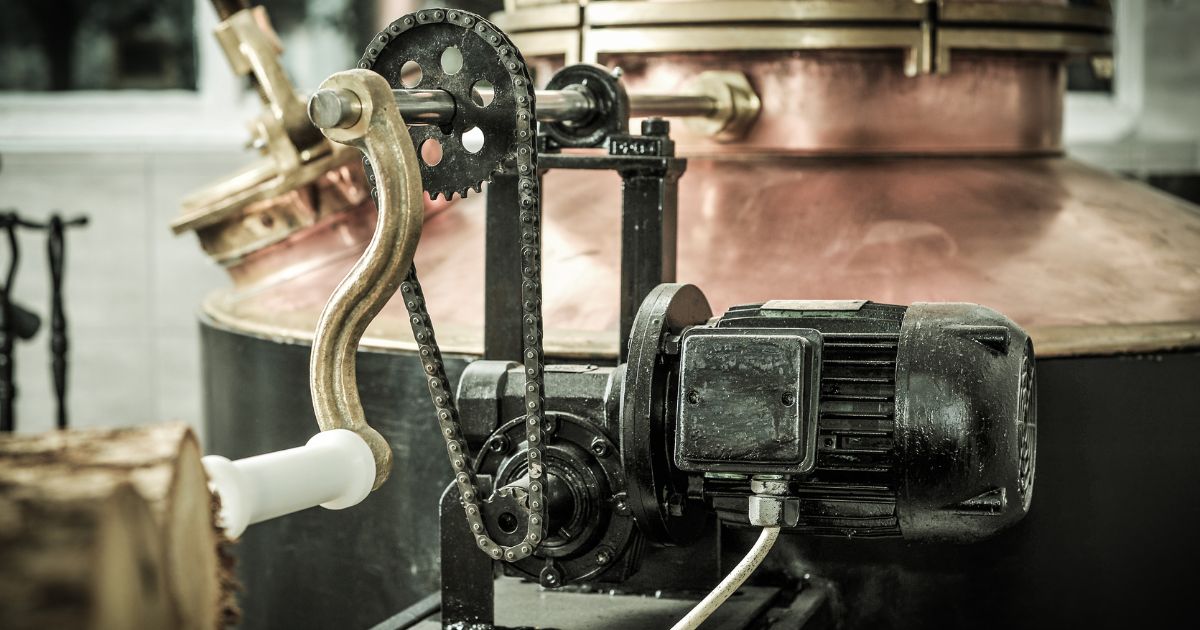
As a follow-up to our Quick Guide to Choosing an Electric Motor article, we attempt to answer the most common questions about hazardous area motors. You might also want to learn more on the factors affecting electric motor lifespan and the common causes of their breakdown.
In this article, we list answers to:
- What is a hazardous area?
- How are hazardous areas classified?
- How is hazardous area equipment classified?
- What relevant certifications and standards should I check?
- How are hazardous area electric motors classified?
- Are flameproof and explosion-proof motors the same?
- What about electric motor IP ratings?
- What belts are best used with electric motors for hazardous areas?
- Which industries commonly have hazardous areas?
- Does AIMS sell electric motors for hazardous areas?
What is a hazardous area?
A hazardous area is broadly defined as a location, place or vicinity where the environment is either alleged or confirmed to have a presence of a chemical spill, dangerous material, explosive element, radiation or a similar substance.
In the context of electric motors, a hazardous area is defined as a space in which (potentially) substances are present -- be it gases, vapours, dust or particles -- that may cause an explosion when exposed to a spark (either from electric wirings or friction from moving parts).
How are hazardous areas classified?
They are classified by zones that indicate where and what potentially explosive substance(s) are present in the atmosphere.
Areas with explosive gas and vapour hazards:
- Zone 0: Combustible gases are likely present either continuously for long periods, or frequently for short periods (more than 1,000 hours per year)
- Zone 1: Combustible gases are likely present occasionally/periodically in normal site operation (more than 10 hours but less than 1,000 hours per year)
- Zone 2: Combustible gases are not likely present in normal site operation but may be present for a short period (less than 10 hours per year)
Areas with explosive dust particles hazards:
- Zone 20: Combustible dust (in cloud form) is likely present either continuously for long periods, or frequently for short periods
- Zone 21: Combustible dust (in cloud form) is likely present occasionally/periodically in normal site operation (more than 10 hours but less than 1,000 hours per year)
- Zone 22: Combustible dust (in cloud form) is not likely present in normal site operation but may be present for a short period (less than 10 hours per year)
How is hazardous area equipment classified?
It is classified into three groups:
- Group I covers electrical equipment for underground mines exposed to firedamp/methane.
- Group II covers electrical equipment in surface-level areas with potentially explosive gas atmosphere, except firedamp/methane. Specifically, it is sub-grouped into:
- IIA: Potential exposure to propane
- IIB: Potential exposure to ethylene
- IIC: Potential exposure to hydrogen
- Group III covers electrical equipment in areas with potentially explosive dust atmosphere.
What relevant certifications and standards should I check?
Check that the electric motor is compliant with standards set out in AS/NZS60079, which is essentially an adaptation of IEC60079 international standards by the International Electrotechnical Commission (IEC).
How are hazardous area electric motors classified?
Through IEC60079 standards, the IEC has defined a system that categorizes and tests "Ex equipment"; that is, equipment designed for safe use in hazardous areas.
In application, electric motors that fit that definition are built such that they won’t cause ambient explosive gases and dust to be ignited.
Some common types:
- Ex d: Flame-proof motors
- Ex e: Increased safety motors
- Ex i: Intrinsic safety motors
- Ex n: Non-sparking motors
- Ex p: Pressurized enclosure motors
- Ex t: Dust ignition protected motors
Are flame-proof and explosion-proof motors the same?
While both are designed to be used in hazardous areas:
- They adhere to different standards.
- Flame-proof motors (the preferred international term) comply with IEC60079-1: Equipment Protection by Flame Proof Enclosures.
- Explosion-proof motors (commonly used in North America) comply with ANSI/UL1203: Explosion-Proof and Dust-Ignition-Proof Electrical Equipment for Use in Hazardous (Classified) Locations.
- They follow different testing parameters (explosion-proof motors undergo more intense testing compared with flame-proof motors).
- Explosion-proof motors are built heavier than flame-proof motors.
What about electric motor IP ratings?
Ingress protection (IP) ratings tell us how well a particular motor unit is protected against solids (eg. dust) and liquids (eg. water spray). They are not to be used as a basis for the safe use of electric motors in hazardous environments.
What belts are best used with electric motors for hazardous areas?
You can further mitigate the risk of explosion by using fire-resistant anti-static (FRAS) belts, like these ones from Pix. As the name implies, these belts are designed to (1) not catch fire from heat build-up and (2) prevent static electricity build-up from friction that may cause sparks to start fire, in a hazardous area.
Which industries commonly have hazardous areas?
You can use this list by WorkSafe Queensland as a reference.
Flammable liquids, vapours and gases
- Gas manufacturing and processing plants
- Gas storage and dispensaries
- Landfill gas recovery plants
- Biogas and fuel plants
- Hydrogen generation plants
- Glue/resin batch plants
- Fiberglass and glass manufacturers
- Hospital operating theatres
- Laboratories
- Bitumen storage tanks (heated >100°C)
- Cement manufacturers
- Landfill sites
- Chemical plants
- Mineral refineries
- Pharmaceutical manufacturers
- Paint warehouses and manufacturers
- Paint mixing and tinting plants
- Printing plants
- Spray booths
- Treated water dosing stations
- Sewage treatment plants
- Petrol stations
- Fuel dispensaries and refineries
- Fuel tanker filling plants
- Fuel storage tanks
- Coal seam gas wells and plants
- Hydrocarbon dewatering plants
- Oil recycling facilities
Combustible dusts
- Industrial bakeries
- Milk manufacturing plants
- Grain storage silos
- Sugar refineries
- Sugar storage silos
- Breweries
- Distilleries
- Flour mills
- Plasterboard manufacturers
- Food manufacturing (industrial scale)
- Coal stockyards
- Coal conveyor transfer chute
- Sawmills
- Fertilizer manufacturing and storage
Does AIMS electric motors for hazardous areas?
Yes, by special order. Please contact us via chat or email and we’ll help you source the correct one for you.
AIMS' Note on Safe Use of Belt-Driven Systems
- Power down: Before any inspection, maintenance, or adjustment, make sure to completely shut down the power to the machine and apply a lockout/tagout (LOTO) device to prevent accidental restarts.
- Right belt for the system: Keep in mind that v-belts (especially cogged / notched / wrapped belts) are different from synchronous /timing / ‘toothed’ belts. Some mistake the cogs for teeth but remember that cogged belts run on V-shaped pulleys that do not have teeth. Are you operating where flammable substances are present? Maybe you need fire-resistant anti-static (FRAS) belts – or maybe heat-resistant and oil-resistant belts will do. We compared them in this FAQ.
- Safe attire: Avoid loose clothing, jewelry and long hair that could get caught in the moving parts. Ensure proper fit of workwear without compromising comfort, dexterity and protection. Tie back long hair and secure loose items.
- Safeguards in place: Never operate a belt-driven system with the guards removed or bypassed. These guards are there for your protection.
- Maintenance and replacement: Regularly inspect belts and pulleys for wear and tear. Maintain proper belt tension and alignment as specified by the manufacturer. When replacing the belt, make sure you get the proper fit and measurement of the system. These accessories and maintenance kits (eg alignment tools, belt measurers, pulley gauge sets, spacers, tensioners etc) come in handy.
- Cleanliness: Keep the area around belt drives free of debris and clutter that could get caught or cause a fire hazard.
(Refer to our content library's sub-index of articles about belt-driven systems and electric motors for more information.)