FAQs on Tap Magic Cutting Fluids
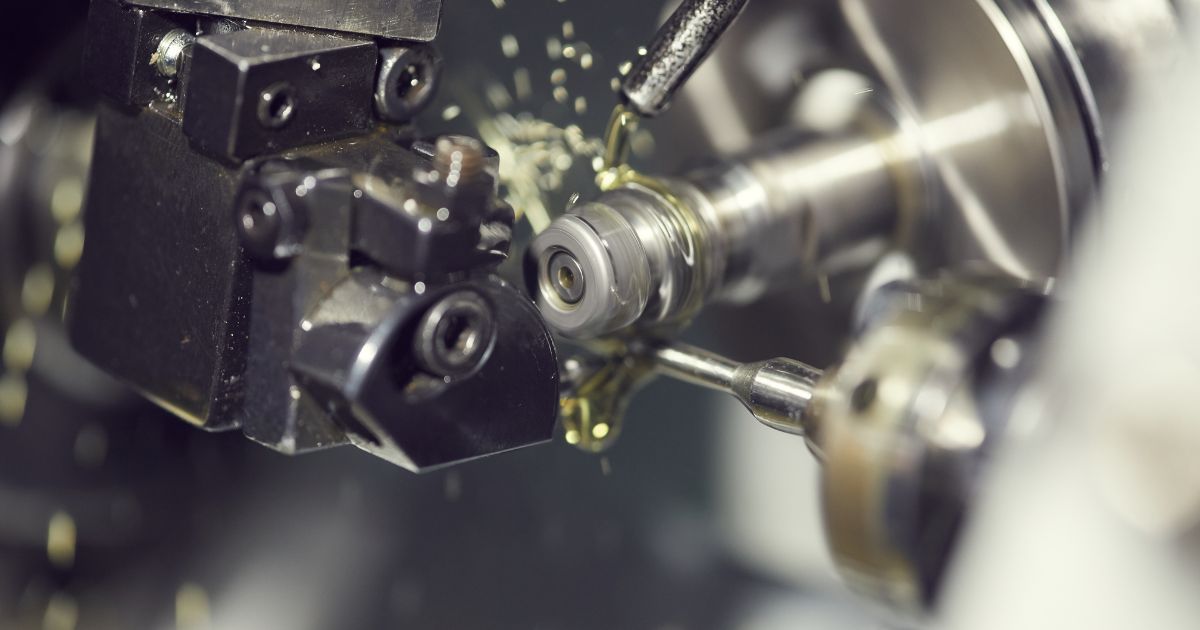
(Taken from this post by Tap Magic. Republished with permission. Edited for point of view, recency and relevance.)
It’s hard to talk about the best cutting fluids in the market without mentioning Tap Magic. We often get these questions from customers that we might as well share the answers from Tap Magic themselves.
- Is there silicone in Tap Magic cutting fluids?
- What is the shelf-life of Tap Magic cutting fluids?
- Where can I buy Tap Magic Original or obtain the SDS for that product?
- Are there any allergens in Tap Magic brand products?
- What is the best way to clean Tap Magic cutting fluid from my tooling and parts after machining?
- How do I get the last bit of product out of the aerosol can?
- What materials are okay to use with Tap Magic products?
- Why would I use Tap Magic Aluminum formula when aluminum is a recommended metal for Tap Magic EP-Xtra or ProTap?
- Can I order Tap Magic products direct from the manufacturer?
Is there silicone in Tap Magic cutting fluids?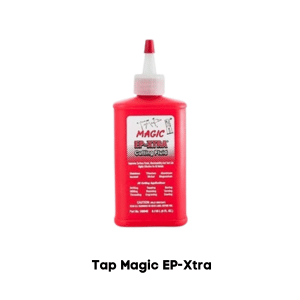
There is no silicone, either as an ingredient or trace contaminant, in any of their cutting fluid formulas. This includes Tap Magic EP-Xtra®, Tap Magic Aluminum, Tap Magic Eco-Oil and Tap Magic Xtra-Thick. The same applies to Tap Magic ProTap, Tap Magic Formula 1 “Aqueous” and Tap Magic Xtra-Foamy.
What is the shelf-life of Tap Magic cutting fluids?
All Tap Magic products have a recommended shelf life of five to eight years depending on storage conditions, with the exception of Tap Magic Eco-Oil which has a recommended shelf life of 18 months.
Other factors, such as the propellant in aerosol cans, may affect the life of the product. Tap Magic may be used well beyond this timeframe but there may be a decrease in performance for protecting your tooling and workpieces.
Where can I buy Tap Magic Original or obtain the SDS for that product?
The Steco Corporation has not manufactured Tap Magic Original since 2007, so that product has no GHS-compliant SDS.
Are there any allergens in Tap Magic brand products?
The Steco Corporation certifies there are no allergens (soy, wheat, eggs, nuts, milk etc) in any of their Tap Magic cutting fluid formulas (or in any of their base ingredients, to their knowledge).
What is t
he best way to clean Tap Magic cutting fluid from my tooling and parts after machining?
Solvent-based chemicals or commercial degreasers -- such as the Tap Magic Cleaner/Degreaser -- work great. Most of all, make sure the cleaner is compatible with your material. Cleaning steel does not protect it from corrosion though. After cleaning, we recommend good shop practices to protect against corrosion and staining of machined surfaces by using a corrosion inhibitor or rust preventative such as the Tap Magic Corrosion Inhibitor.
Note: Leaving “spent” fluid on tools and work-pieces for extended lengths of time is not recommended.
How do I get the last bit of product out of the aerosol cans?
Occasionally, it can be difficult to get the last few drops of Tap Magic out of an aerosol can. If this happens, try twisting the nozzle ¼ turn; this will realign the spray tube inside the can so that it contacts the liquid when the can is tilted at 45 degrees again. If the first turn does not work, try another ¼ turn; continue to move it around until liquid sprays out.
What materials are okay to use with Tap Magic products?
Occasionally, it can be difficult to get the last few drops of Tap Magic out of an aerosol can. If this happens, try twisting the nozzle ¼ turn; this will realign the spray tube inside the can so that it contacts the liquid when the can is tilted at 45 degrees again. If the first turn does not work, please try another ¼ turn; continue to move it around until liquid sprays out.
Why would I use Tap Magic Aluminum formula when aluminum is a recommended metal for Tap Magic EP-Xtra or ProTap?
Any of these formulas can be used in aluminum machining operations. With some alloys of aluminum or brass, the metal can be very soft causing galling or tool buildup in some applications. The advantage of Tap Magic Aluminum in this situation is that it has special additives in the formula to minimise this phenomenon. If one of the other formulas works well on the soft metal you machine, there is no need to make a change. But if you experience the issue, try Tap Magic Aluminum and you just might be pleased with the results!
Can I order Tap Magic products direct from the manufacturer?
The Steco Corporation currently sells its products through a network of premium distributors that add value to their customers.
(If you’re reading this, then you are probably in Australia, and we at AIMS Industrial Supplies carry their products as distributor and retailer in the country.)
AIMS' Note on Managing Chips
- Tool geometry: Choose cutting tools with chipbreakers designed for the material you're machining. These chip-breakers introduce interruptions or curves into the cutting edge, forcing the chips to curl and break into smaller, more manageable pieces. Also, selecting the correct nose radius for your insert can help control chip formation.
- Cutting parameters: Adjust your feed rate and cutting speed. Increasing feed rates often helps break chips, while higher cutting speeds can produce thinner and more manageable chips. However, be careful not to push speeds and feeds beyond the tool's capabilities, as this can lead to tool breakage or poor surface finish. Refer to recommended parameters from your tooling manufacturer as a starting point.
- Coolant: High-pressure coolant directed at the cutting zone can effectively break chips and flush them away, improving chip control. Ensure your coolant system is working optimally and use the correct coolant type for the job.
- Machine rigidity: A rigid machine setup helps reduce vibrations that can lead to unpredictable chip formation. Make sure your workpiece and tooling are clamped securely to minimise unwanted movement.
- Disposal: Dispose of used abrasives properly per local regulations.