FAQs on Welding Safety
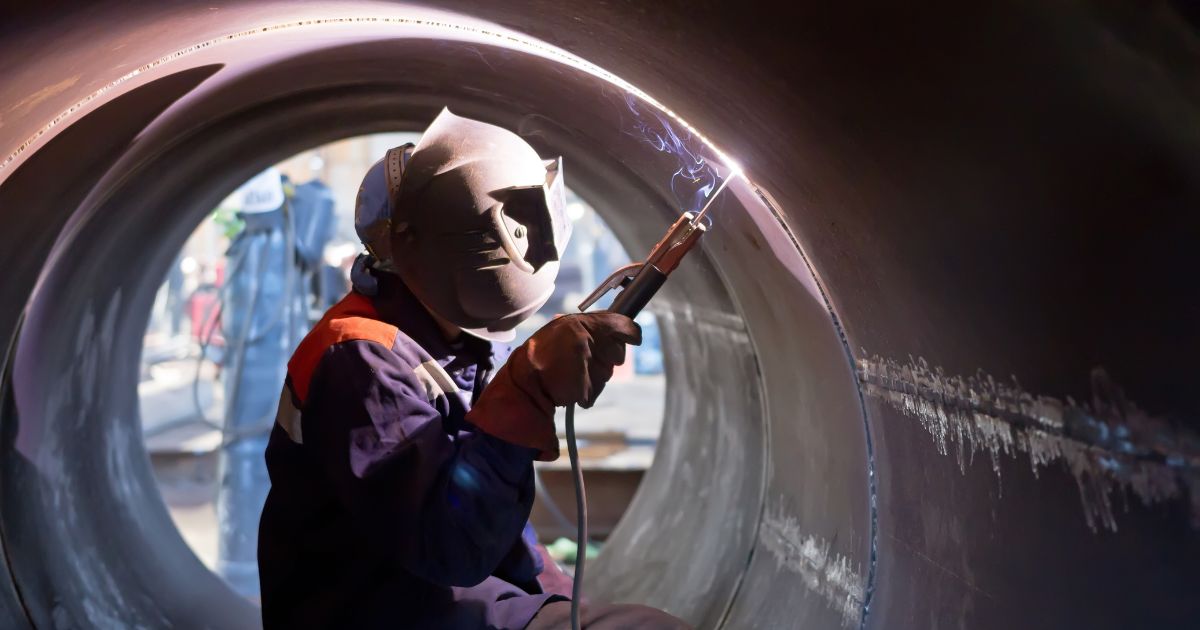
In this article, we answer these questions:
- What are the key hazards associated with welding?
- What is the Australian Standard for welding safety?
- What are the primary control measures for welding hazards?
- What PPE is needed for welding?
- What is the Workplace Exposure Standard (WES) for welding fume in Australia?
- How bad can welding fumes be?
- How bad can flash burns be?
- What are my responsibilities for welding safety?
- Are there specific safe welding codes of practice per state?
What are the key hazards associated with welding?
Here are the most common ones:
- Fumes and harmful gases: Welding generates fumes that can contain harmful (and even cancerous) substances and inhaling them can lead to short and long-term health issues, including respiratory problems and potential cancers.
- Electric shock: Welding equipment uses electricity, thereby posing a risk of electric shock, particularly in damp or wet conditions. Faulty equipment or improper grounding also increases this risk.
- Burns: The welding arc, sparks and hot metal can cause severe burns, so best make sure to wear PPE properly.
- Eye injuries: UV and infrared radiation from the welding arc can damage eyes, leading to conditions such as "arc eye" (aka flash burns) or permanent vision loss.
- Fire and explosions: Welding sparks can ignite flammable materials, particularly in some welding processes that use flammable gases.
What is the Australian Standard for welding safety?
AS/NZS 1764 provides the overarching framework for welding safety in Australia, including requirements for risk assessment, hazard control and worker training. Specifically:
- AS/NZS 1674.1:1997 Safety in welding and allied processes – Part 1: Fire precautions is the current designation that outlines specific safety guidelines for welding and similar processes that pose fire and explosion risks. It emphasizes a hierarchy of control measures to minimise risk, namely elimination/substitution, isolation, engineering and administrative controls and personal protective equipment (PPE).
- AS/NZS 1674.2:2007 Safety in welding and allied processes – Part 2: Electrical is the current designation that outlines specific safety guidelines for welding and similar processes that pose electrical hazards.
Other relevant standards:
- AS/NZS 1338.1:2012 Filters for eye protectors, Part 1: Filters for protection against radiation generated in welding and allied operations covers the shade recommendations for welding helmets relevant to the welding process.
- Safe Work Australia Codes of Practice: Specific codes of practice exist for managing welding processes, hazardous chemicals, noise and confined spaces, all of which are relevant to welding safety. Refer to the full text of SWA’s Model Code of Practice on Welding Processes for more comprehensive information.
What are the primary control measures for welding hazards?
According to SWA’s Model Code of Practice on Welding Processes (published July 2020, that is the most recent version to date), businesses can manage the risks associated with welding by implementing these control measures wherever possible:
- Elimination and substitution: Do away with welding altogether or at least substitute the activity with a less hazardous process. For instance, fabrications may include pre-cast components or extruded shapes to eliminate the need to weld. Bolting is another (more common) alternative to welding.
- Isolation: Limit how much contact people have with the hazard by moving the work to a separate remote location, or at least by using barriers (such as these welding blankets and curtains) to block off the dangerous area.
- Engineering controls: Implement physical modifications to the workspace that are designed to minimise risk, such as local exhaust ventilation (LEV) systems to capture the fume at its source.
- Administrative controls: Consider implementing changes to work procedures that are designed help reduce danger. Some suggestions include (1) limit welding time, (2) rotating welders and (3) allowing for frequent breaks to lower the welder’s risk of heat exhaustion (more on working in heat in this article). Of course, those are on top of the adequate training and compliance to safe work procedures that are expected of you.
- PPE: Mandate the use of appropriate respiratory protection, welding helmets, protective clothing and gloves. In some instances, the welder may have to stand on metallic surfaces which form part of the electric circuit that may become ‘live’, so making them wear work shoes with electrical hazard protection will reduce the risk of electric shock.
Important: Administrative controls and PPE are reactive and do not eliminate the hazard itself, and they heavily depend on people to follow rules and wear the right gear.
What PPE is needed for welding?
Here is a more complete list of safety wearables on top of the examples we provided above:
- Welding clothing: They are specially made to protect the body from sparks and heat, and many of them are made of flame-retardant materials. You can choose from a variety of welder’s jackets. At the minimum, at least wear some leather sleeves and full aprons to protect your skin from spatter. Snoods also work to protect the head and neck.
- Welding gloves: They are designed to protect your hands from burns / flames / heat, electrical shocks / sparks and ultraviolet rays from the welding process.
- Welding goggles and face shields: They protect your eyes from the dangers of welding, including heat, sparks and harmful radiation. The googles use dark lenses, rated by shade number, to let you see your work safely. Higher shade numbers mean darker lenses and more protection. In addition, welding face shields are extra protection worn over goggles. They have clear visors to shield your face from sparks and debris during welding and similar tasks.
- Welding helmets: They protect your eyes and face from arc radiation, sparks and debris. You can choose between auto-darkening and fixed shade variants. Choose one with the appropriate level of shade for the welding process and a wide viewing area for optimum convenience. Accessories and supplementary parts are also available to help you keep them in top shape.
- Respiratory protection: They prevent workers from inhaling airborne hazardous substances. A secure fit is vital for preventing leaks.
Pro tip: You can also use anti-spatters to, well, reduce spatter and get cleaner welds.
What is the Workplace Exposure Standard (WES) for welding fume in Australia?
In January 2024, Safe Work Australia (SWA) announced that “Work Health and Safety Ministers have agreed to an immediate reduction to the workplace exposure standard (WES) for welding fumes (not otherwise classified) has been reduced from an 8-hour time weighted average (TWA) of 5 mg / m3 to 1 mg / m3.”
- Such a reduction is believed to better protect workers from the adverse health effects associated with welding fumes, such as lung cancer.
- This stricter standard requires a revision of risk assessments and implementation of additional ventilation and respiratory protection measures.
How bad can welding fumes be?
According to SafeWork NSW, in 2017 the International Agency for Research on Cancer (IARC), a part of the World Health Organization, found enough evidence to declare welding fumes a definite cause of cancer. They also classified UV radiation from welding as a cancer-causing agent for the first time.
Welding fumes are full of particles you obviously don’t want to inhale:
- Tiny metal pieces: Welding fumes are full of microscopic bits of the metal you’re working with during welding. Think beryllium, chromium, cadmium, manganese, nickel and the like.
- Dangerous gases: Welding also releases gases -- such as ozone, nitrogen oxides and even carbon monoxide – that can irritate your airways or be seriously poisonous.
You don’t want to deal with these health problems, especially #4 onwards which have long-term negative effects:
- Breathing troubles such as coughing, wheezing and trouble catching your breath
- Irritated eyes and skin that make it hard for you to function properly and focus on the task at hand
- Metal fume fever that makes you feel achy and sick like you have the flu
- Compromised lungs that generally weaken your immunity and make it harder for you to breathe
- Brain problems caused by inhaled manganese that may cause symptoms similar to Parkinson's Disease
- Cancers (usually of the lung, kidney and the larynx / voice box, but there could be more) that everybody wants to avoid
Pro tip: Refer to this informative fact sheet (with a snapshot below) by The Cancer Council to learn more about the occupational cancer risks of welding:
Note: The specific type of welding process, metals involved and ventilation in the workplace all influence the risk level. So do individual factors like genetics and smoking habits that make some people more susceptible to the carcinogenic effects of welding fumes.
How bad can flash burns be?
Arc eye or flash burns, also known as photokeratitis, can range from mildly uncomfortable to extremely painful and potentially dangerous.
It’s also sometimes referred to as welder’s flash, and it is often caused by the bright light and UV rays from welding, so make sure to wear welding goggles at the minimum.
According to a Queensland Health Emergency Department fact sheet, it feels like having grit in your eyes with the following symptoms:
- Pain that may be mild to very severe
- Bloodshot eyes
- Being sensitive to light
- Watery eyes
- Blurred vision
Better Health Channel by Victoria’s Department of Health indicates that treatment could involve:
- Eye drops
- Coverings to rest your eyes
- Cool packs
- Artificial tears
- Antibiotics
Important: While mild cases get better on their own, severe ones need immediate medical attention to prevent complications like temporary vision loss or infection.
What are my responsibilities for welding safety?
That heavily depends on your role, but always keep in mind that safety is always a shared responsibility.
Employers and Persons Conducting Business Undertakings (PCBUs)
- Primary duty of care: You ensure the health and safety of all workers and others who might be affected by the work.
- Provide a safe workplace: This includes safe systems of work, appropriate equipment that is well-maintained and a suitable work environment.
- Manage risks: You must conduct thorough risk assessments for welding operations, implement the control measures mentioned above (and then some) and regularly review them to make sure they are ever relevant to your current circumstances. This includes processing of hot work permits.
- Information, training, instruction and supervision: Provide comprehensive training on welding procedures, hazard identification, safe use of equipment and emergency responses. Ensure workers are adequately supervised.
- Consultation: Actively involve workers in identifying hazards and developing safety solutions.
- Risk assessments: Conduct thorough risk assessments of all welding operations.
- Safe Work Procedures: Develop and enforce clear procedures for safe welding.
- Equipment Maintenance: Maintain welding equipment in good condition.
- Emergency Plans: Prepare for welding-related emergencies (fires, explosions, injuries).
Workers
- Take reasonable care: Protect your own health and safety and that of others.
- Follow safety procedures: Adhere to established work practices and instructions provided by your employer.
- Wear and use PPE correctly: Make sure you use them appropriately and they fit you properly.
- Report hazards and incidents: Immediately notify your supervisor about any safety concerns, near-misses or accidents so they can immediately be reviewed, and their risks mitigated so they can immediately be reviewed, and their risks mitigated
- Participate in safety initiatives: Actively engage in training, risk assessments and safety discussions.
Are there specific safe welding codes of practice per state?
We compiled these links based on current information (as of March 2024):
New South Wales:
Northern Territory:
- https://ablis.business.gov.au/service/nt/welding-processes-code-of-practice/46263
- https://worksafe.nt.gov.au/forms-and-resources/codes-of-practice/welding-processes2
Queensland:
- https://ablis.business.gov.au/service/qld/welding-processes-code-of-practice-2021/42275
- https://www.worksafe.qld.gov.au/safety-and-prevention/hazards/hazardous-exposures/welding
Western Australia:
- https://ablis.business.gov.au/service/wa/australian-standard-as-1674-safety-in-welding-and-allied-processes/17568
- https://www.commerce.wa.gov.au/publications/code-practice-welding-processes
South Australia:
- https://ablis.business.gov.au/service/sa/welding-processes-code-of-practice/43568
- https://www.safework.sa.gov.au/workplaces/work-tasks-and-projects/welding
Tasmania:
- https://ablis.business.gov.au/service/tas/welding-processes-code-of-practice/31087
- https://worksafe.tas.gov.au/__data/assets/pdf_file/0020/537131/Code-of-Practice-Welding-processes.pdf
- https://worksafe.tas.gov.au/topics/laws-and-compliance/codes-of-practice/cop-folder/welding-processes
Victoria:
AIMS’ Note on Buying Industrial Supplies
- Breadth and depth of brands and categories: Go with a supplier that offers a wide range of reputable brands across multiple categories and sub-categories.
- Bulk purchase discounts: For large orders, check if you can take advantage of volume leverage. Some suppliers offer business accounts* that give you access to special pricing (volume discounts), preferential support and even credit eligibility (subject to supplier approval, terms and conditions).
- Product and service information: Evaluate the completeness and usefulness of data in their online product listings. Prudent suppliers will include as much useful information as possible to help you assess and compare products. In terms of service info, the supplier’s FAQs (if any) will give you a good idea of their standard policies*, processes and commitments.
- Promotions: Check for ongoing promotional campaigns so you can get the best prices. Many suppliers run regular discount-based promos. Some can point you to government-hosted rebate programmes like the SafeWork NSW $1000 Small Business Rebate.
- Safety compliance: Make sure the product in question meets Australian safety standards and regulations, especially if there are relevant compliance requirements or work health and safety (WHS) laws that apply to your business or state. Look for relevant certifications and markings where necessary.
- Supplier reliability: Choose reputable suppliers with a proven track record of delivering quality products and reliable customer service.
- Warranty and support: Check warranty terms and after-sales support* options, as this can be crucial in case of product defects or performance issues.
- Lead time and availability: Confirm product availability and estimated delivery times to avoid delays in your projects.
- Returns: Familiarise yourself with the suppliers returns and exchange policy in case you receive incorrect or damaged items.
- Delivery: Clarify delivery terms, including estimated delivery times, shipping costs and who handles insurance during transit (where applicable).
*Need help with a purchase decision? Contact us directly via chat or send an email to sales@aimsindustrial.com.au.