Tips and Tools to Tackle Stripped Threads
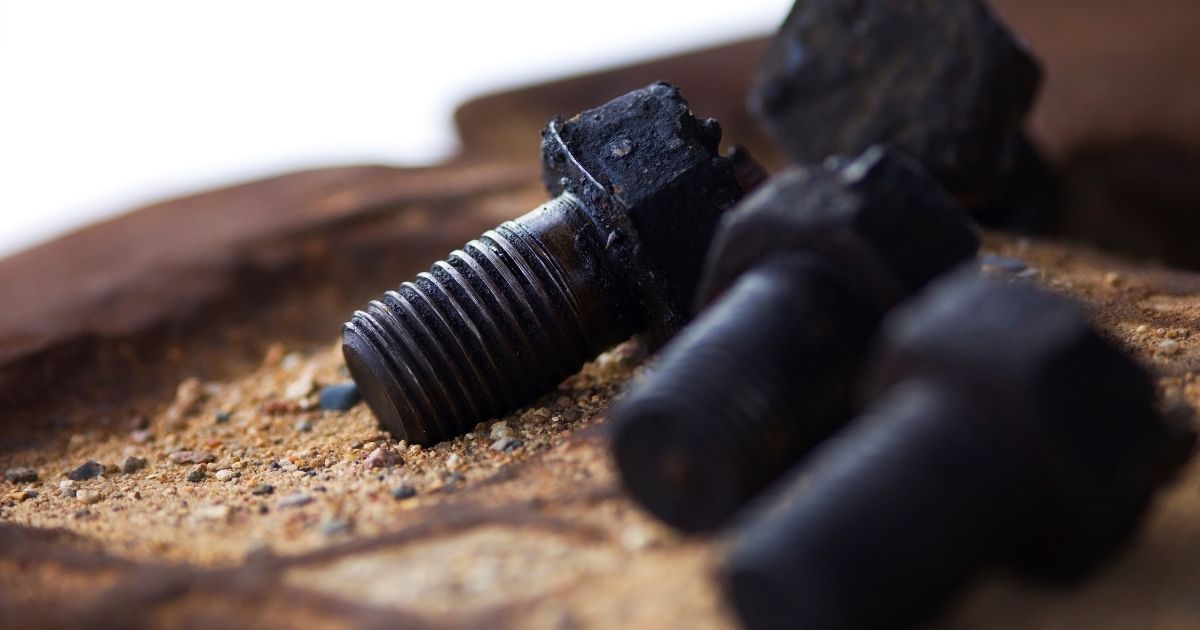
(Taken from this post by Champion Parts. Republished with permission. Edited for point of view and relevance.)
Most of us have had to deal with damaged threads, but when an internal thread becomes unserviceable it can be a real issue.
Stripped threads happen more when dealing with alloy components such as cylinder heads and manifolds.
Sometimes, you have no choice but to keep to the original thread size rather than just tapping out to a bigger size.
Champion Parts offers a range of thread repair kits to cover the most popular thread sizes. The kits usually come with a drill, tap, insert and break-off tool and a range of different length stainless steel coil inserts to suit the desired thread length.
Here’s a quick guide to how you can deal with stripped threads:
To start the process, choose the length of the thread coil required for the job, use the HSS drill bit from the kit (Fig. 1 and 2). Drill out the damaged thread deeper than the coil being used to allow for the tap to cut a good thread for the entire length of the coil (Fig. 3). With the tap supplied from the kit tap out the hole to the required length for the coil, use a good lubricant to help this part of the process to go smoothly (Fig. 4).
Place the coil to be used on the insert tool with the cross pin at the end to be inserted into the hole first, or it will not work (Fig. 5 and 6). With some downward pressure start screwing the insert into the tapped hole. This process does take some effort to start but keep screwing in the insert until it is just under the edge of the surface (Fig. 7).
Now, insert the break-off tool into the inserted coil. It will stop at the cross pin. With a hammer, give the break-off tool a tap and the pin will break off.
Now your job is complete, just clean up and you can get back to reassembling your job using the original fastener size (Fig. 8).
Tips
-
For a successful result, it is crucial that you make sure you are using the correct size drill for the tap. (If you need help selecting the correct size drill, we can send you this handy Wall Chart FREE courtesy of Sutton Tools. You just cover the postage costs.
-
You can slightly chamfer or countersink the hole prior to drilling for a better-looking result.
-
To determine how deep to tap, use a texter to mark the depth the tap has to go by placing the coil against the tap with the bottom of the coil starting where the taper on the tap finishes.
-
The insert will appear too big, but it will fit.
-
Make sure you always clean up the swarf and broken off pin to prevent damage down the track.
AIMS' Note on Safe Use of Hand Tools
- Inspection: Before using any tool, carefully inspect it for cracks, chips, loose handles, worn / mushroomed heads or any other signs of damage. Damaged or defective tools may cause harm! Ensure all guards are in place.
- Right tool for the job: Make sure you understand the intended purpose of each tool and choose the correct one for your specific job. Don't try to make a screwdriver work as a pry bar or a wrench as a hammer.
- Safe handling: Carry sharp tools pointed down and away from your body. Never carry tools in your pockets where they can cause injury. When passing a tool to someone, extend the handle first.
- PPE: Wear safety glasses or goggles to protect your eyes from flying debris. Consider gloves depending on the tool and task to prevent cuts or blisters but without compromising comfort, dexterity and protection. If working with noisy tools, wear ear protection.
- Maintenance: Keep your tools clean, sharp and properly maintained. Store them in a safe and organised place when not in use.