Understanding Basic Diameters in Tapping Drill Sizes
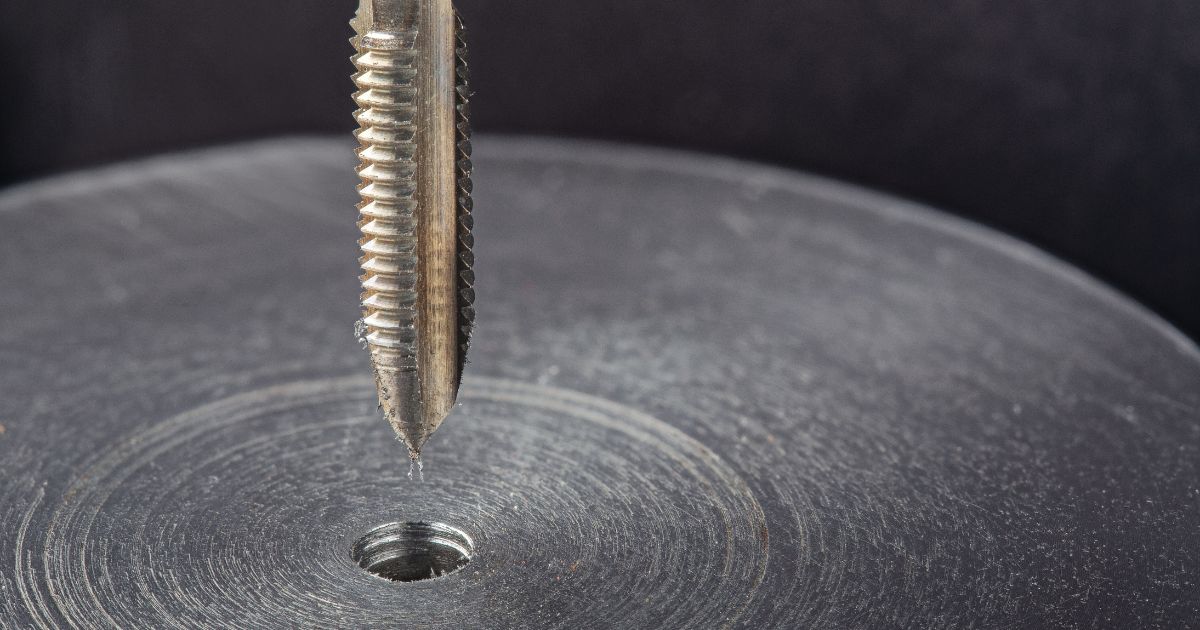
Basic diameters in threading
When discussing tapping drill sizes and thread dimensions, we primarily deal with three basic diameters:
- Major diameter: This is the largest diameter of the thread, measured across the outer peaks of the thread profile
- Minor diameter: This is the smallest diameter of the thread, measured across the roots of the thread profile.
- Effective diameter: This is an intermediate diameter, often used in thread calculations, and is typically defined as the average of the major and minor diameters. However, its precise definition can vary depending on the specific thread standard.
Notes:
- In threading taps, effective diameter and pitch diameter are essentially the same thing.
- They both refer to the diameter of an imaginary cylinder that intersects the threads where the width of the threads equals the width of the spaces between them
- This imaginary cylinder is essentially the "meat" of the thread, where most of the engagement and strength come from.
Relationship to tapping drill size
The tapping drill size is closely related to the minor diameter of the thread. When drilling a hole for tapping, the drill bit should create a hole slightly larger than the minor diameter to accommodate the thread formation.
- For metric threads: A common rule of thumb is to subtract the thread pitch from the major diameter to estimate the tapping drill size. However, this is a simplified approximation, and actual tapping drill sizes are often listed in tap drill charts for specific thread standards.
- For inch threads: The tapping drill size is often calculated as a percentage of the major diameter, with different percentages used for coarse and fine threads.
Importance of accurate tapping drill size
Selecting the correct tapping drill size is crucial for achieving proper thread formation and ensuring the strength and durability of the threaded joint. An undersized hole can lead to thread stripping, while an oversized hole can result in a weak thread.
Notes:
- The specific calculations and factors influencing tapping drill size can vary depending on the thread standard (eg metric, UNC, UNF etc), thread class, material and desired thread depth.
- It's essential to refer to appropriate tap drill charts and engineering standards for accurate and reliable results.
- Choosing the right tap (tap type, flute design, material etc) for the application is equally important.
AIMS' Note on Safe Use of Power Tools
- Inspection: Before using any tool, carefully inspect it for cracks, chips, loose handles, worn / mushroomed heads or any other signs of damage. Damaged or defective tools may cause harm! Ensure all guards are in place.
- Right tool for the job: Make sure you understand the intended purpose of each tool and choose the correct one for your specific job. Don't try to make a screwdriver work as a pry bar or a wrench as a hammer.
- Safe handling: Carry sharp tools pointed down and away from your body. Never carry tools in your pockets where they can cause injury. When passing a tool to someone, extend the handle first.
- PPE: Wear safety glasses or goggles to protect your eyes from flying debris. Consider gloves depending on the tool and task to prevent cuts or blisters but without compromising comfort, dexterity and protection. If working with noisy tools, wear ear protection.
- Maintenance: Keep your tools clean, sharp and properly maintained. Store them in a safe and organised place when not in use.
- During use: Maintain a firm grip and good balance while using the tool. Avoid distractions and focus on the task. Don't force the tool; let it work at its own pace. Keep cords clear of the cutting path and away from heat or sharp objects. Never leave a running tool unattended. When finished, turn the tool off, unplug it, and wait for any moving parts to stop completely before cleaning or making adjustments.