Tapping Drill Size Chart for Thread Cutting Taps (Metric-Imperial Equivalents)
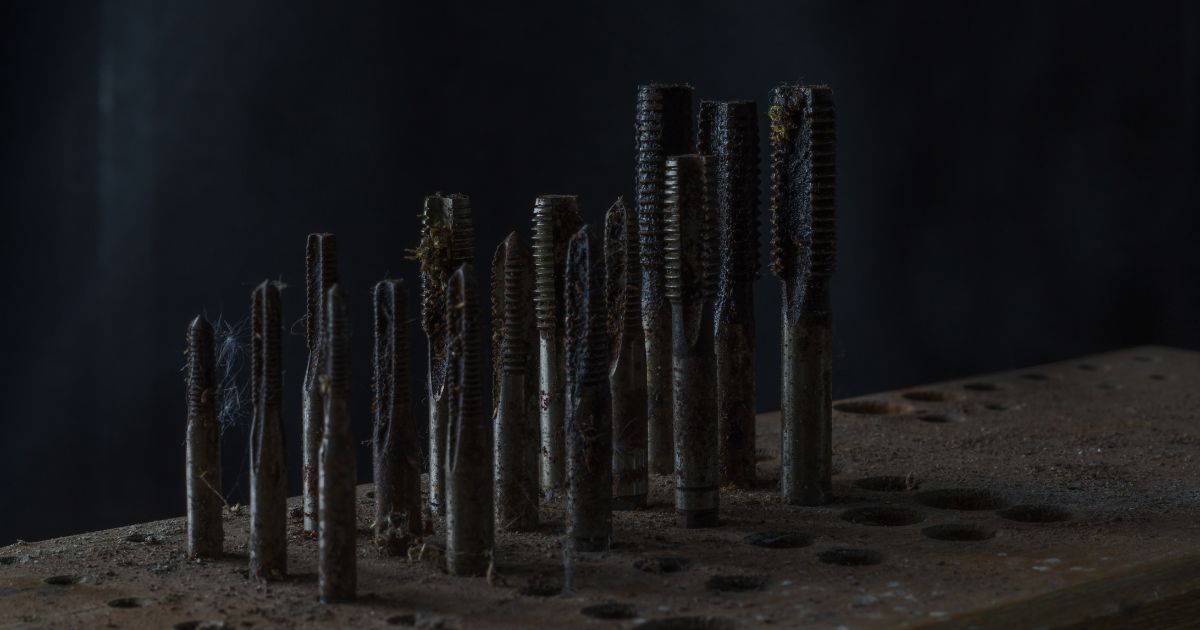
This tapping drill size chart primarily provides essential information to determine the correct drill size for creating a pilot hole before cutting threads with a tap. This ensures that the tap has enough material to cut into and produce accurate, strong threads to help in:
- Preventing tap breakage: Drilling a hole that is too small can cause the tap to break.
- Ensuring thread quality: A properly sized hole ensures that the threads are formed correctly and have the desired strength.
- Optimizing tapping process: Using the correct drill size improves efficiency and reduces the risk of errors.
By accurately matching the tap size to the drill size and choosing the right tap for the job, you can achieve optimal results in your thread cutting operations.
We trust that the information below is self-explanatory and straightforward.
Tap / Thread Size | ISO Metric COARSE (Tapping Drill = TD) | ISO Metric FINE (Tapping Drill = TD) | ||||||||||||
Metric (mm) | Pitch (mm) | TD (mm) | TD (decimal inches) (~) | Fractional inches (~) | # | Pitch Values* (mm) | TD (mm) | |||||||
M1.0 | 0.25 | 0.75 | 0.03 | --- | #67 | --- | ||||||||
M1.2 | 0.25 | 0.95 | 0.037 | --- | #61 | --- | ||||||||
M1.4 | 0.30 | 1.10 | 0.043 | --- | #55 | --- | ||||||||
M1.6 | 0.35 | 1.25 | 0.049 | 3/64 | --- | --- | ||||||||
M1.8 | 0.35 | 1.45 | 0.059 | --- | #53 | --- | ||||||||
M2.0 | 0.40 | 1.60 | 0.063 | --- | #52 | 1.75 | ||||||||
M2.2 | 0.45 | 1.75 | 0.070 | --- | #50 | --- | ||||||||
M2.5 | 0.45 | 2.05 | 0.081 | --- | #46 | 2.15 | ||||||||
M3.0 | 0.50 | 2.50 | 0.098 | --- | #37 | 2.65 | ||||||||
M3.5 | 0.60 | 2.90 | 0.114 | --- | #32 | --- | ||||||||
M4.0 | 0.70 | 3.30 | 0.130 | --- | #29 | 0.50 | 3.50 | |||||||
M4.5 | 0.75 | 3.70 | 0.146 | --- | #25 | 0.50 | --- | |||||||
M5.0 | 0.80 | 4.20 | 0.165 | --- | #16 | 0.50 | 4.50 | |||||||
M6.0 | 1.00 | 5.00 | 0.197 | --- | #8 | 0.75 | 5.30 | |||||||
M7.0 | 1.00 | 6.00 | 0.236 | --- | B | 0.75 | 6.25 | |||||||
M8.0 | 1.25 | 6.75 | 0.268 | --- | H | 0.75 | 1.00 | 1.25 | 7.00 | |||||
M9.0 | 1.25 | 7.75 | 0.305 | --- | #31 | 0.75 | 1.00 | 1.25 | --- | |||||
M10.0 | 1.50 | 8.50 | 0.335 | --- | R | 0.75 | 1.00 | 1.25 | 9.00 | |||||
M11.0 | 1.50 | 9.50 | 0.374 | --- | #9 | 0.75 | 1.00 | --- | ||||||
M12.0 | 1.75 | 10.25 | 0.402 | --- | Y | 1.00 | 1.25 | 1.50 | 10.50 | |||||
M14.0 | 2.00 | 12.00 | 0.472 | 15/32 | --- | 1.00 | 1.25 | 1.50 | 12.50 | |||||
M16.0 | 2.00 | 14.00 | 0.551 | 9/16 | --- | 1.00 | 1.50 | 14.50 | ||||||
M18.0 | 2.50 | 15.50 | 0.61 | 39/64 | --- | 1.00 | 1.50 | 2.00 | 16.50 | |||||
M20.0 | 2.50 | 17.50 | 0.689 | 11/16 | --- | 1.00 | 1.50 | 2.00 | 18.50 | |||||
M22.0 | 2.50 | 19.50 | 0.768 | 49/64 | --- | 1.00 | 1.50 | 2.00 | 20.50 | |||||
M24.0 | 3.00 | 21.00 | 0.827 | 53/64 | --- | 1.00 | 1.50 | 2.00 | 22.00 | |||||
M27.0 | 3.00 | 24.00 | 0.945 | 61/64 | --- | 1.00 | 1.50 | 2.00 | --- | |||||
M28.0 | --- | --- | --- | --- | --- | 1.00 | 1.50 | 2.00 | --- | |||||
M30.0 | 3.50 | 26.50 | 1.043 | 1-1/16 | --- | 1.50 | 2.00 | 3.00 | --- | |||||
M33.0 | 3.50 | 29.00 | 1.161 | 1-1/8 | --- | 1.50 | 2.00 | 3.00 | --- | |||||
M36.0 | 4.00 | 32.00 | 1.26 | 1-1/4 | --- | 1.50 | 2.00 | 3.00 | --- | |||||
M39.0 | 4.00 | 35.00 | --- | 1-3/8 | --- | 1.50 | 2.00 | 3.00 | --- | |||||
M42.0 | 4.50 | 37.50 | 1.476 | 1-1/2 | --- | 2.00 | 3.00 | 4.00 | --- | |||||
M45.0 | 4.50 | 40.50 | 1.594 | 1-5/8 | --- | 2.00 | 3.00 | 4.00 | --- | |||||
M48.0 | 5.00 | 43.00 | 1.693 | 1-3/4 | --- | 2.00 | 3.00 | 4.00 | --- | |||||
M50.0 | 5.00 | 45.50 | 1.772 | 1-7/8 | --- | 48.50 |
The reason for multiple fine pitch values in tapping threads is to provide more flexibility in design and application. Fine pitch threads offer greater flexibility in design and application due to several key advantages. By providing multiple fine pitch options, you can select the most appropriate pitch for your specific application according to these factors:
Strength and weight:
- Fine pitches provide higher thread strength due to increased contact area.
- However, they require more material removal, potentially increasing weight.
- Ideal for applications where strength is paramount but weight is less critical.
Tolerance requirements:
- Fine pitches offer tighter tolerances for thread form and fit.
- Beneficial for applications requiring precise alignment or interference fits.
Thread depth and hole size:
- Allow for deeper threads within a given hole size.
- Useful when thread depth is crucial but hole size is constrained.
Vibration and shock:
- Less susceptible to vibration and shock due to tighter thread fit.
- Suitable for applications subject to dynamic loads.
Aesthetic considerations:
- Can create a more refined or delicate appearance compared to coarse pitches.
More Considerations:
- The choice of drill size and thread depth can vary significantly based on the material being tapped (eg steel, aluminium, plastic).
- The desired thread depth affects the necessary clearance for the tap.
- The tightness of the thread (close, medium, or free fit) influences the drill size.
- Different tap types (taper, plug, bottoming) require slightly different drill sizes.
- The Engineers Black Book’s section in calculation of tapping drill sizes advises to “use a good cutting oil or lubricant rather than coolant for fluteless (thread forming) taps”.
Notes:
- This table covers a range of sizes but might not include all available thread sizes.
- Not all metric tapping drill bits have imperial equivalents, and vice versa.
- Fine thread sizes are less common than coarse threads.
- Coarse or fine threads require different drill sizes.
- Some metric values are close enough to essentially have the same imperial counterpart.
- Some values are rounded to their nearest thousandth millimeters and ten-thousandth decimal inches.
Important:
- Always consult a detailed tap drill chart for accurate and precise drill size selection.
You may want to consider getting the Engineers Black Book (3rd Edition – Metric) for more complete information, specifically:
- Calculation, formulas and examples of tapping drill size:
- For thread cutting taps (tapping drill size in metric and inches, thread percentage in metric)
- For fluteless taps (tapping drill size in metric and inches)
- Complete and detailed tapping drill sizes (screw size, major/minor/ effective diameters, tap and clearance drill sizes etc) for thread cutting taps in:
- ISO metric coarse, metric fine, metric conduit, metric special pitches and metric sparkplug
- UNC (Unified National Coarse)
- UNF (Unified National Fine)
- UNEF (Unified National Extra Fine)
- BA (British Association)
- BSW (British Standard Whitworth)
- BSF (British Standard Fine)
- BSP (British Standard Pipe)
- BSPT (British Standard Pipe Taper)
- PG (Panzerrohr-Gewinde)
- NPT (American National Pipe Taper)
- Illustrations
- Thread cutting and thread forming taps
- Tap geometry
- Tap chamfers
- Thread percentage and tap selection (for workpiece material, eg hard steel, cast iron etc)
More size charts
- Anchor Bolt Size Chart: Sort through a wide variety of metric anchor bolt types: countersunk head sleeve anchor, drop-in anchor, hex flange nut sleeve anchor, flush head sleeve anchor and stud anchor. Common metric diameters listed.
- Drill Bit Size Chart: Choose the right bit size to ensure a proper fit for your intended gauge sizing. Metric (SI) and imperial (US decimal / fractional inches) values matched.
- Fastener Reference Chart: Cross-reference the measurement of your bolt, nut or screw with these comprehensive table of sizes. Metric, Unified Thread Standard and British Thread Standards values matched. There are also simplified illustrations of how to identify metric or imperial fasteners by thread pitch and threads per inch, respectively.
- Loctite Application Chart: Know which Loctite product to use with various materials and surfaces, from bricks and ceramics to vinyl and wood.
- Pulley Size Chart: Sort through a wide variety of aluminium and cast-iron pulleys for different belt sections and grooves. For taper locks, pilot bores and bores with keyway. Metric and imperial sizes available.
- Socket Sizing Cross-Reference Chart (Metric-Imperial Values): Match the right (or nearest alternative) sockets and drives. Metric and imperial sizes available.
- Spanner Size Chart: Find out which spanner size to use for your bolt, nut or screw with a hexagonal head. Metric and imperial (UNC/UNF) sizes matched.
AIMS' Note on Safe Use of Power Tools
- Inspection: Before using any tool, carefully inspect it for cracks, chips, loose handles, worn / mushroomed heads or any other signs of damage. Damaged or defective tools may cause harm! Ensure all guards are in place.
- Right tool for the job: Make sure you understand the intended purpose of each tool and choose the correct one for your specific job. Don't try to make a screwdriver work as a pry bar or a wrench as a hammer.
- Safe handling: Carry sharp tools pointed down and away from your body. Never carry tools in your pockets where they can cause injury. When passing a tool to someone, extend the handle first.
- PPE: Wear safety glasses or goggles to protect your eyes from flying debris. Consider gloves depending on the tool and task to prevent cuts or blisters but without compromising comfort, dexterity and protection. If working with noisy tools, wear ear protection.
- Maintenance: Keep your tools clean, sharp and properly maintained. Store them in a safe and organised place when not in use.
- During use: Maintain a firm grip and good balance while using the tool. Avoid distractions and focus on the task. Don't force the tool; let it work at its own pace. Keep cords clear of the cutting path and away from heat or sharp objects. Never leave a running tool unattended. When finished, turn the tool off, unplug it, and wait for any moving parts to stop completely before cleaning or making adjustments.