Quick Guide to Industrial Gloves
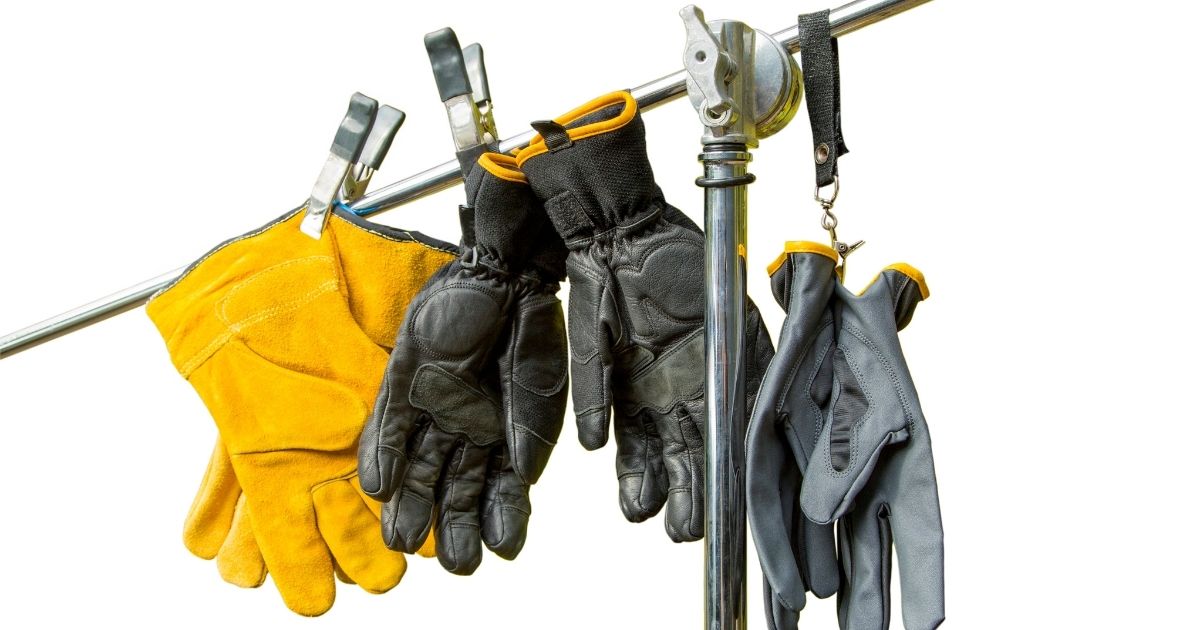
We can’t emphasise enough that everyone should take work, health and safety (WHS) seriously.
It’s not just a recommendation – it’s the responsibility of businesses and persons conducting a business or undertaking (PCBUs) to ensure that risks of physical injuries and deaths are mitigated across the board.
There are even state laws to govern WHS in Australia.
In this article, let’s take a closer look at hand protection, specifically gloves:
- Why industrial gloves are important
- Which glove is right for the job
- Different types of industrial gloves
- Standards and protection ratings
(While this article is directed at business owners and department managers, the information presented here is equally applicable to you if you are an industrial glove user. For example, if you’re a tradesman or MRO worker buying gloves for yourself.)
Why industrial gloves are important
Industrial gloves -- also called safety gloves and work gloves -- are personal protective equipment (PPE) meant to secure a user’s hand from possible harm, often in the context of performing their trade or work.
Their general purpose is to provide hand protection from common workplace hazards in common light-duty applications, such as cleaning, packing, maintenance work and warehousing. Of course, there are special gloves made for heavy duty scenarios as well.
Materials from which gloves are made vary depending on their intended application.
Wearing proper gloves can help you and your workers prevent:
- Loss of fingers (or even hands)
- Punctures and abrasions
- Cuts and bruises
- Slipping
They can also protect your hand from:
- Extreme temperatures (or sudden, drastic changes thereof)
- Absorption of dangerous chemical substances
- Uncomfortable vibrations
- Electric conduction/shock
- Burns
Which glove is right for the job?
These questions can guide your choice from the perspective of WHS Management:
- What are the hand safety standards in the area where your business operates?
- Do you have a safety record that documents previous hand-related injuries? There will be guidance in there on how you could avoid such incidents. There should already be recommendations about what specific PPE is needed for certain tasks.
- Do you have a documented safety policy that governs your decision when buying gloves?
- Do you know how to properly inspect gloves?
- Do you have special safety considerations, such as if your workers work in:
- Power distribution, where they deal with high voltage power lines
- Construction, where they operate heavy machinery and power tools
- Oil and gas, where they handle equipment and tools in a potentially slippery environment (where the equipment and tools they hold can be easily covered in oil)
- Laboratories, where they process potentially dangerous biohazards, chemicals and microorganisms
Also, consider things from the perspective of the end-user (your workers):
- Are they working in places where there are a lot of hand hazards?
- Does the job require dexterity and tactility?
- Does the job require accurate finger movement with the gloves on, such as pushing small buttons on a control panel and touching screen controls with precision?
- Do they have a personal preference when it comes to safety gloves?
- Are they allergic to certain materials? Many gloves are made of latex and rubber, and some people are allergic to them.
Important: Beware of overprotection. Thicker and heavier is not always better. Being too wary may lead you to get gloves that are way bulkier than is ideal in certain work situations. Bulkier gloves may have an impact on how well a worker can perform a task and ultimately be less safe.
Practical advice:
- The end-users' opinions matter: On paper, one kind of glove may seem superior to another, but those who will wear it may have a different and more practical view. You don’t want to buy gloves that end up not being used because they’re so impractical and uncomfortable that they’d rather risk injury by not wearing them.
- Size matters: Gloves must fit well and be comfortable to wear, otherwise it may discourage the user from keeping them on. Too big and they may fall off; too small and they may cause extreme discomfort.
- Replace the gloves as needed: Worn-out gloves can lose their overall effectiveness to protect the hands. Also, sweat accumulates on the inside. You can throw some gloves in the laundry, but you may compromise their quality and fit. So, err on the side of caution, especially when it comes to applications where hand protection is critical.
Different types of industrial gloves
Here are some of the most common gloves classified according to their utility:
- Chemical resistant gloves are designed to withstand chemical degradation when exposed to acids, bases, solvents, and other corrosive substances. They are commonly used in chemical handling and food handling activities.
- Cold resistant gloves are designed to insulate hands from low temperatures while working outdoors or in cold storages. These are suited to handling cold substances, such as dry ice and liquid nitrogen, without hampering comfort and productivity. They are commonly used in cold storage facilities.
- Cut resistant gloves are designed to protect the wearer from skin cuts and punctures. These are cut-and-sewn from cut-resistant materials like aramid (Kevlar®), high-performance polyethylene (HPPE), polyvinyl acetate (PVA), or fiberglass yarns. They meet EN388 standards, and are commonly used in automotive assembly, glass handling, mining and construction.
- Disposable gloves are designed to protect hands from the environment and to prevent the wearer from contaminating the handled products or the workspace. They are commonly used in medical applications and food services.
- General purpose gloves are designed to protect the wearer from workplace hazards, such as cuts, abrasion, scrapes, and dirt in light-duty applications. They are usually made from plain fabric or coated with synthetic rubbers for added chemical protection and gripping power.
- Heat resistant gloves are designed to protect the user from burns and other hazards when working with hot objects. These gloves are rated to EN407 standards with a six-digit number that represents the resistance to flammability, contact heat, convective heat, radiant heat, small splashes of molten metal, and finally resistance to large splashes of molten metal. They are commonly used in foundries, boilers, refineries, ovens, and other applications involving flames or sparks.
- Mechanics gloves are designed to protect mechanics from oil, dirt, grime, grease and other hazards from handling car parts. These provide additional grip for holding oily/greasy car parts/tools and protect the hands from direct skin contact with irritants and hard-to-remove lubricants.
- Rigger gloves are designed to protect hands in rigging and cable pulling. They are generally made from or reinforced with leather that provides protection from abrasion, cuts, and impact. They meet EN388 standards and, thanks to their durability, are highly versatile and commonly used in construction, engineering and maintenance work.
- Vibration resistant gloves or anti-vibration gloves are designed to protect wearers from repetitive impact or vibration that may lead to hand-arm vibration syndrome (HAVS) and other injuries. These are made with layers of vibration dampening polymers to safeguard the user while using pneumatic tools, chainsaws or jackhammers. They meet EN388 standards to protect the hand against mechanical risks and meet resistance to abrasion, cut, tear, and puncture.
Standards and protection ratings matter
Not all gloves are created equal, so make sure you get the right one according to the applicable standard.
You can tell a glove’s protective properties by the markings and symbols printed on the glove itself.
Shown is the marking for a Frontier cut-resistant glove
Here’s a list of the most commonly used standards in gloves, as compiled from various sources and the Beaver Brands PPE catalogue (page 73):
- EN420 (AS/NZS 2161.2:1998) [Superseded by AS/NZS 2161.2: 2005]: This is considered the general “baseline” requirements for protective gloves. This standard is based on the European Standard EN420, and does not apply to electrical, mechanical and medical gloves. This standard applies to ALL safety gloves and requires, amongst other things, packaging to include information about glove size, dexterity and design category.
EN388 (AS/NZS 2161.3:1998) [Superseded by AS/NZS 2161.3: 2005, then ultimately by the current standard AN/NZS 2161.3:2020]: This Standard applies to all kinds of protective gloves giving protection from mechanical risks, in respect of physical problems caused by abrasion, blade cut, tearing or puncture. It also covers the risk of electrostatic discharge. There are four digits displayed alongside this pictogram. Each digit identifies the performance level on a scale of 0 to 5 against four hazards in this order:
- Abrasion Resistance
- Blade Cut Resistance
- Tear Resistance
- Puncture Resistance
EN374 (ANS/NZS 2161.10:2005): This Standard specifies the capability of gloves to protect the user against chemicals and/or micro-organisms.
-
EN407 (ANS/NZS 2161.4:1999): This Standard specifies thermal performance for protective gloves against heat and/or fire.
-
-
EN511 (AS/NZS 2161.5:1998): This Standard applies to gloves which protect the hands against convective and contact cold.
-
-
EN421 (AS/NZS 2161.1:2005): This Standard sets out test methods and performance criteria for gloves offering protection against ionising radiation and radioactive contamination.
The pictograms / symbols are typically accompanied by a series of characters (that contain letter, numbers, or both) with corresponding classifications.
For instance, the pictogram for EN374 is accompanied by at least three characters each of which corresponds to a certain classified chemical. For example, ‘A’ is for methanol and ‘B’ is for acetone. For chemical risk gloves, performance levels are measured on a scale of 1 to 6 to indicate how quickly the hazardous chemical may come into contact with the skin through the glove. This is known as breakthrough time. Performance level 1, for example, means the liquid can permeate the glove within 10 minutes, and level 6, means the chemical will not come into contact with the skin for at least 480 minutes.)
In a nutshell
- Mandating the wearing of proper industrial gloves is important for obvious reasons: protection and compliance.
- Beware of overprotection.
- Find the right balance between protection, comfort and dexterity.
- The wearer’s preference and unique needs matter, too.
- Mind the standards and protection ratings marked on the gloves.
There’s literally no one-size-fits-all when it comes to buying industrial gloves.
AIMS' Note on Buying PPE and Workwear
- Hazard assessment: Identify the specific hazards you will likely be facing in your work environment. Consider potential risks such as chemical exposure, falling objects, loud noises, electrical hazards or biohazards. This assessment will guide you in selecting the appropriate PPE for the job.
- Appropriate materials: Different materials offer various protective qualities. Consider flame-resistant (FR) materials for fire hazards, chemical-resistant fabrics for handling hazardous liquids and high-visibility options for work in low-light environments.
- Compliance to occupational safety standards: Opt for PPE that meets the pertinent Australia Standard (AS), although some brands -- especially imports -- will have other compliance markings such as ANSI, OSHA, ANSI, NIOSH, oSA etc. Look for certifications on the product label to ensure the equipment has undergone rigorous testing.
- Proper fit and comfort: Proper fit is crucial for both comfort, dexterity and protection. Ill-fitting clothing can snag on machinery or restrict movement, potentially creating additional hazards. Choose sizes that allow for layering in cold weather without being overly bulky and consider adjustable options for items like hard hats or respirators.
- Maintenance and replacement: Inspect PPE before each use for signs of wear, tear or damage. Follow (and factor in) the manufacturer's instructions for cleaning and storage. Some materials may require specialised laundering, while others can be machine-washed. Check for durability to ensure the clothing can withstand frequent use and cleaning. Replace damaged or expired PPE immediately to guarantee your safety.
- Training: Ensure you and any employees understand how to properly use, wear, adjust, maintain and store PPE and workwear. Improper use can negate its protective benefits.